Materials engineer
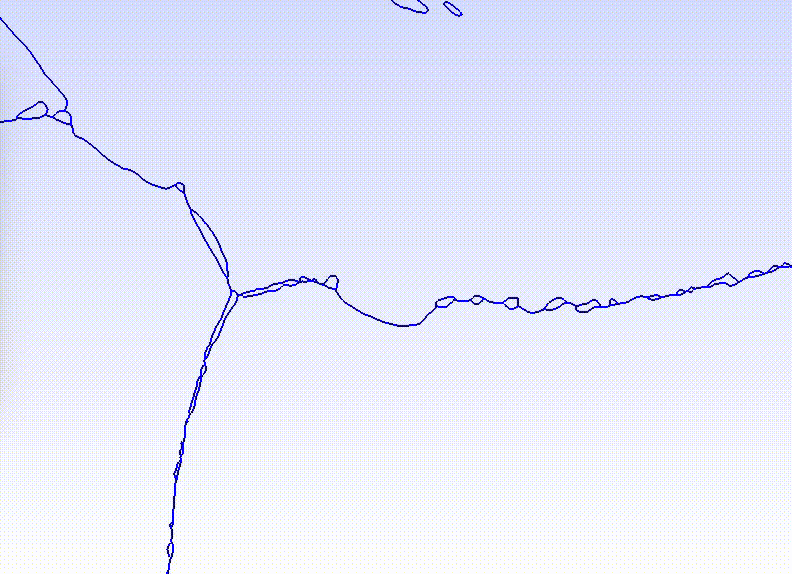
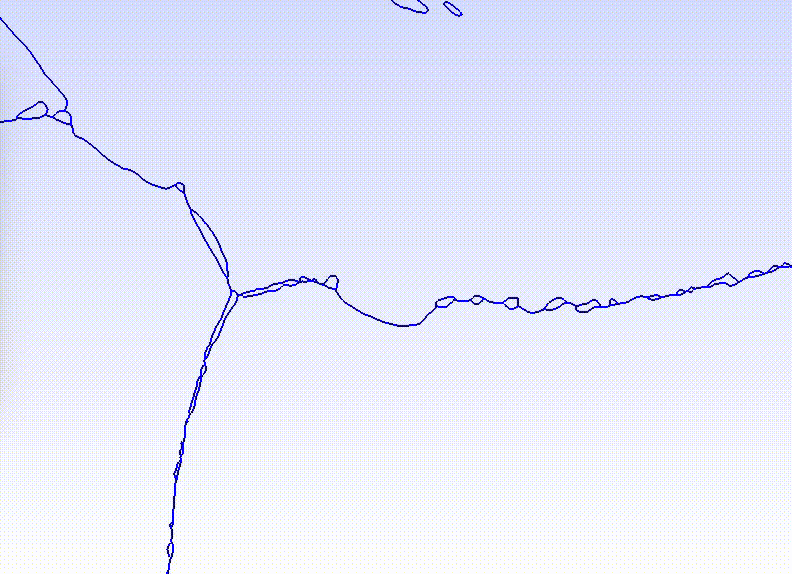
Specialist in computational simulation and mechanical testing |Materials engineer | Test Engineer | FEA | CAE
About me
Materials Engineer specialized in mechanical testing and materials simulation
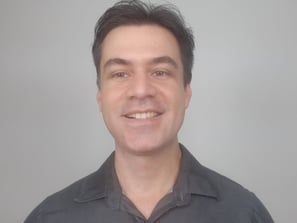
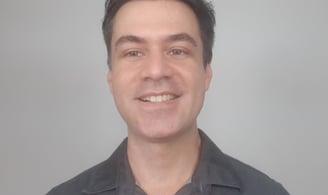
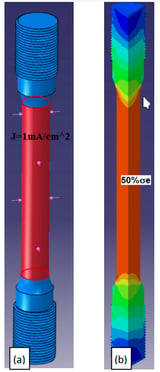
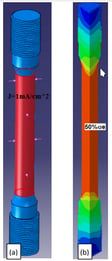
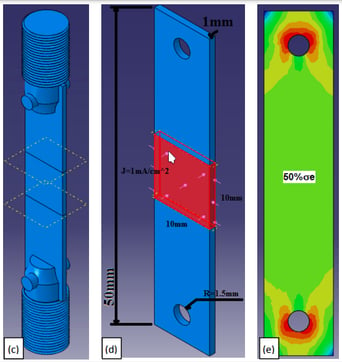
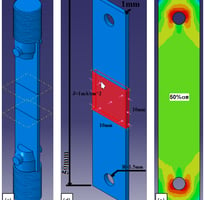
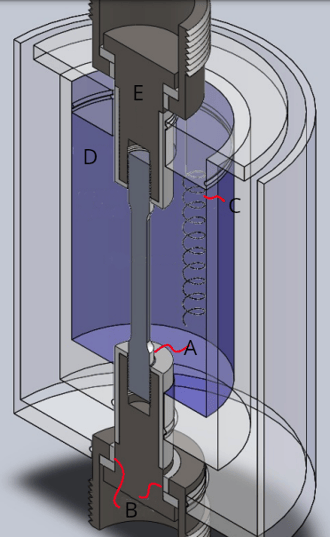
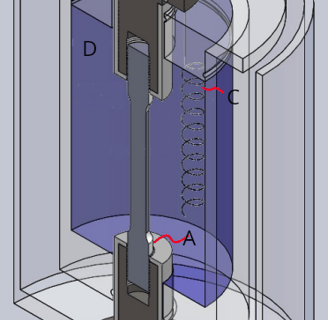
Designing accessories for testing materials in aggressive and corrosive environments is crucial in materials engineering. The complexity lies in creating accessories that can withstand corrosive agents while maintaining structural integrity. Despite the challenges, well-designed accessories are essential for accurate testing, reflecting real-world conditions and enabling precise assessments of material performance in harsh environments.
Fig. 1. Fig. Schematic Drawing of Mechanical Designs for Laboratory: An Example
Fig. 2. Schematic drawing of samples designs for laboratory and simulations: An Example
Materials Engineer specialized in mechanical testing and simulation. Design and develop tools for mechanical testing in hydrogen and/or stress corrosion environments.
Experience
MSc Materials and Metallurgy Engineering
Materials Engineering Specialist - 2019 - 2023 · 4 yrs
Development of solutions for mechanical tests in environments with hydrogen. Adaptations and solutions of test tools. Production of reports and test methods for mechanical tests of fracture and tension with hydrogen. Selection and evaluation of materials for use in the oil and gas industry.
SUSCEPTIBILITY TO JOINT HYDROGEN BRITTLEMENT WELDED FROM 2.25Cr-1Mo STEEL
2009 – 2011
Career history
Analysis of hydrogen embrittlement in Zr alloys applied in Nuclear Industry. Simulation of the thermocalc phases and simulation of the mechanical processing in the DEFORM of the zirconium alloys, Control of the fusion process of the zirconium alloys, Lamination of the alloys and microestructural characterization of the alloys, mathematical simulation of the diffusion in systems.
Materials Engineering Specialist - 2016 - 2018 · 2 yrs
Materials Engineering Specialist - 2016 - 2023 · 6 yrs
Micro mesh generations
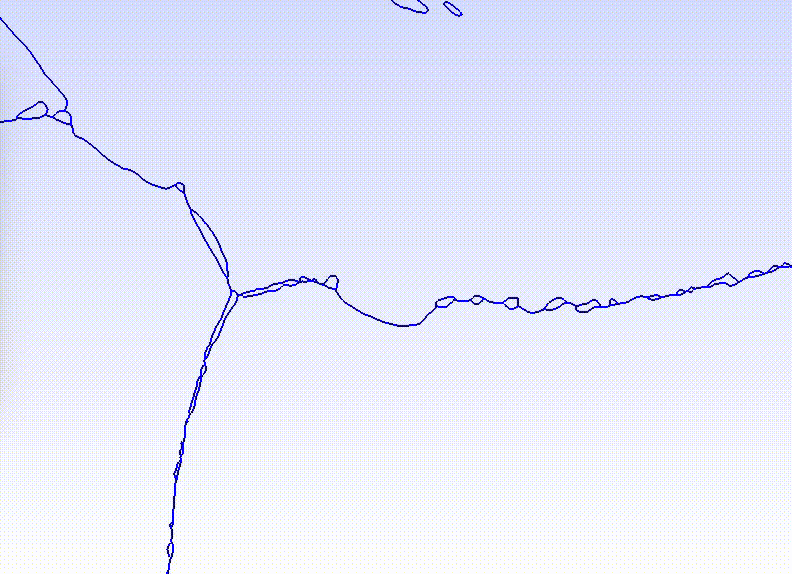
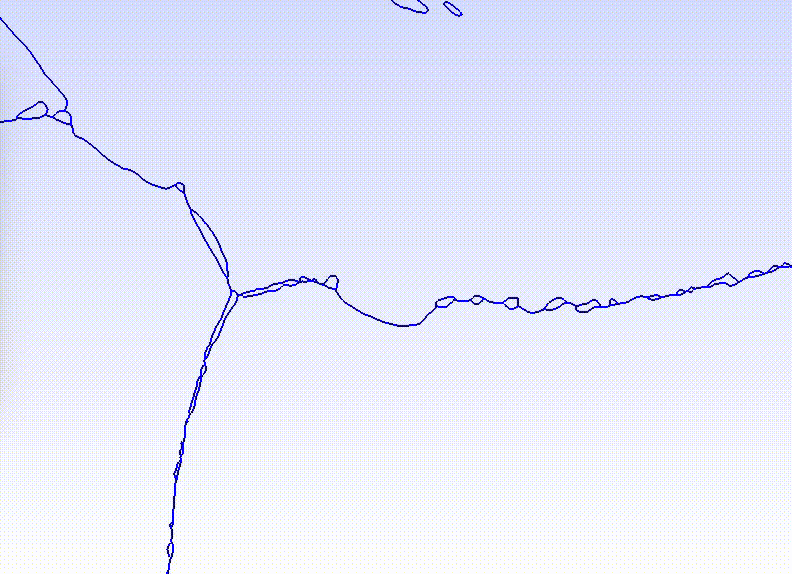
Skills and advancement simulation
In materials engineering, the design of finite element meshes for microstructures holds paramount importance in the overall analysis. This intricate process involves breaking down complex microstructural features into smaller elements, influencing the accuracy of finite element simulations. The challenge lies in striking a balance between achieving a fine resolution to capture microstructural nuances and maintaining computational efficiency. Crafting an effective mesh is crucial for an accurate representation of material behavior, considering factors such as grain boundaries and defects. Despite its significance, mesh design can be a complex undertaking, requiring careful consideration of elements like distortion, size variation, and computational costs. Navigating these challenges is essential for ensuring the reliability and relevance of the final analysis of microstructures in materials engineering.
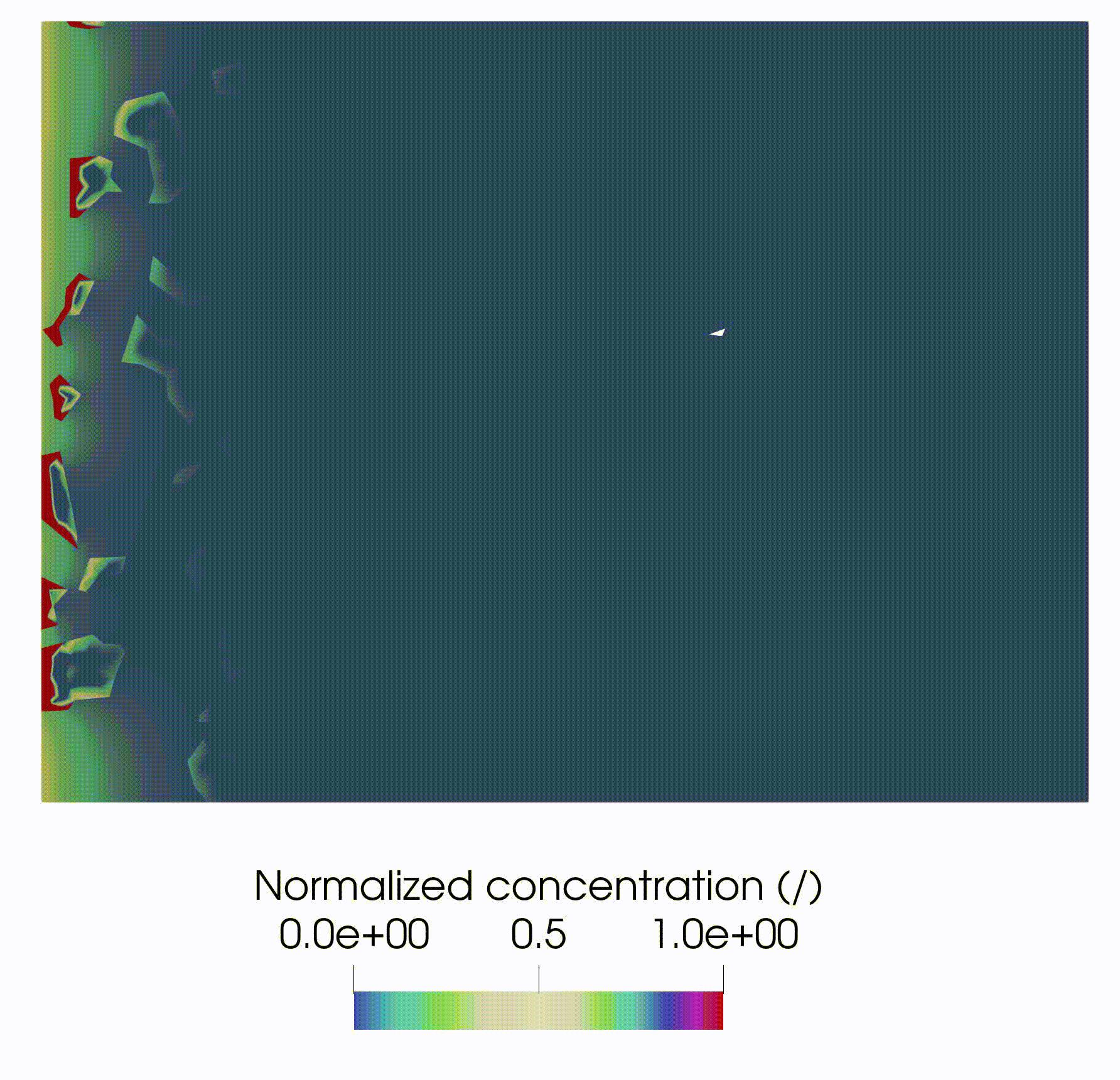
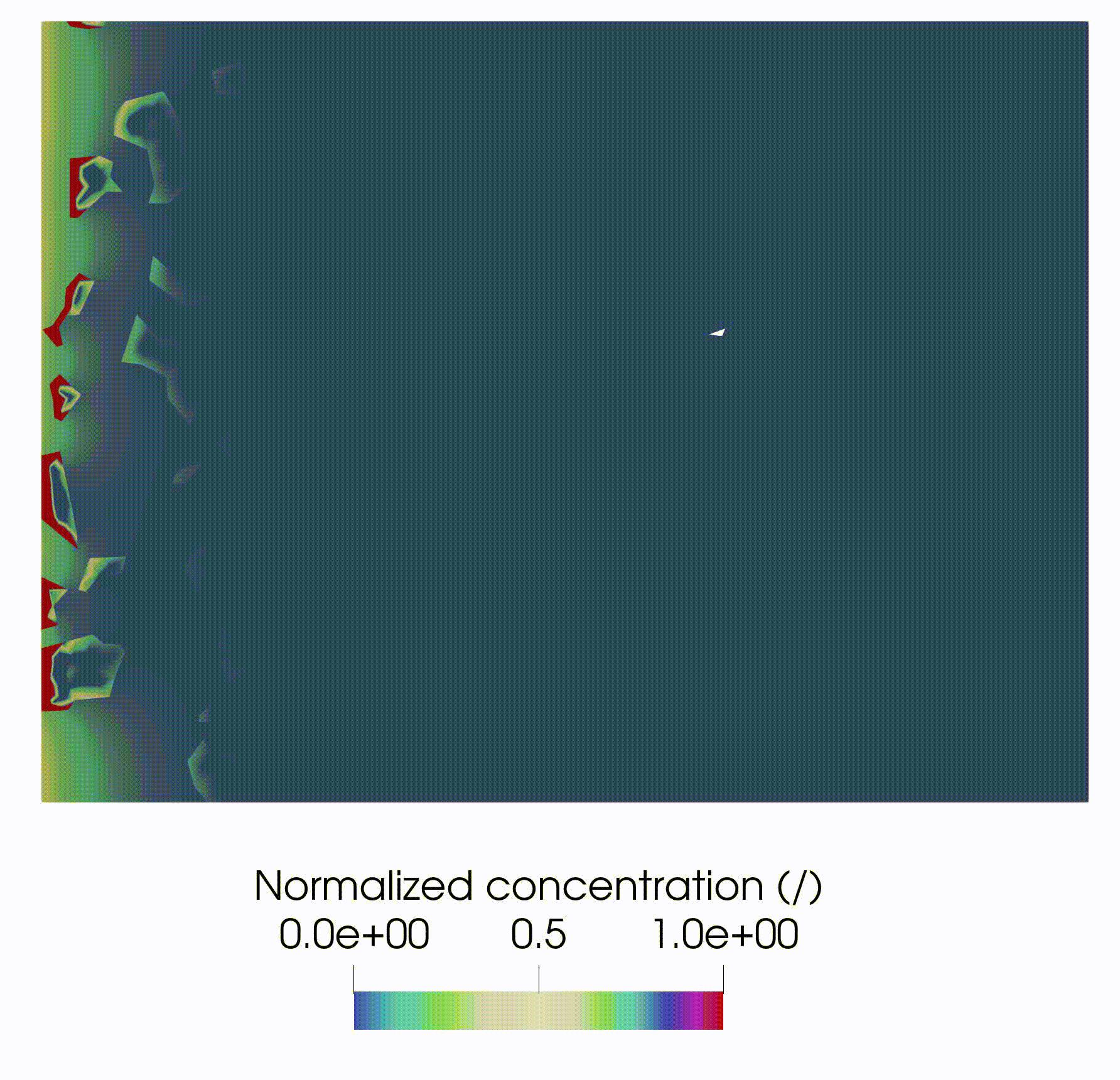
Microstructure simulation
Simulation of finite elements at the microstructural level is a crucial aspect of materials engineering. This approach involves applying finite element methods to model and analyze the behavior of materials at a microscopic scale. By considering the intricate details of a material's internal structure, such as grain boundaries, defects, and inclusions, engineers can gain valuable insights into the material's mechanical properties and performance. This microstructural simulation in materials engineering is particularly useful for predicting how materials will respond to different conditions, aiding in the design and optimization of advanced materials for various applications.
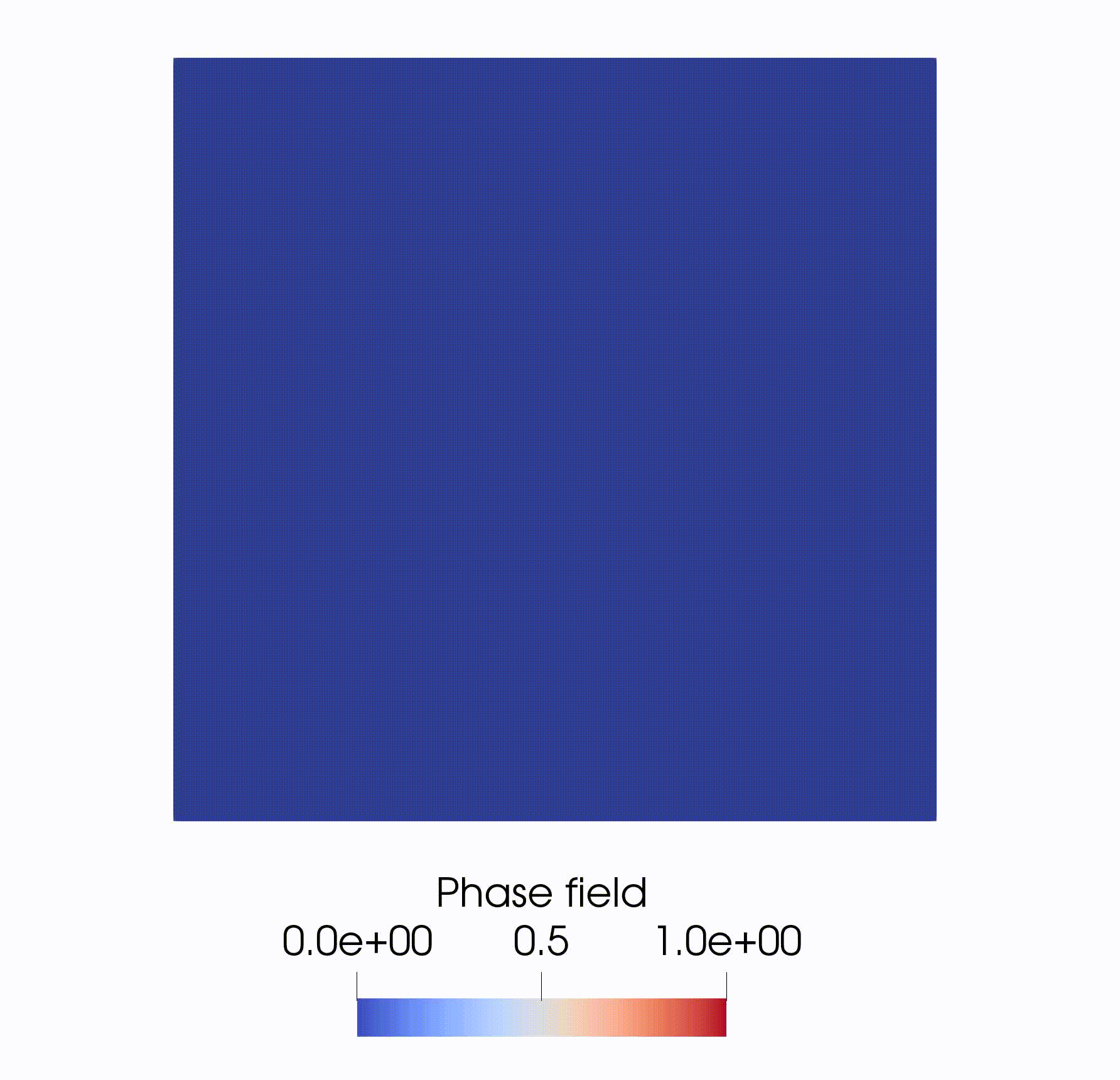
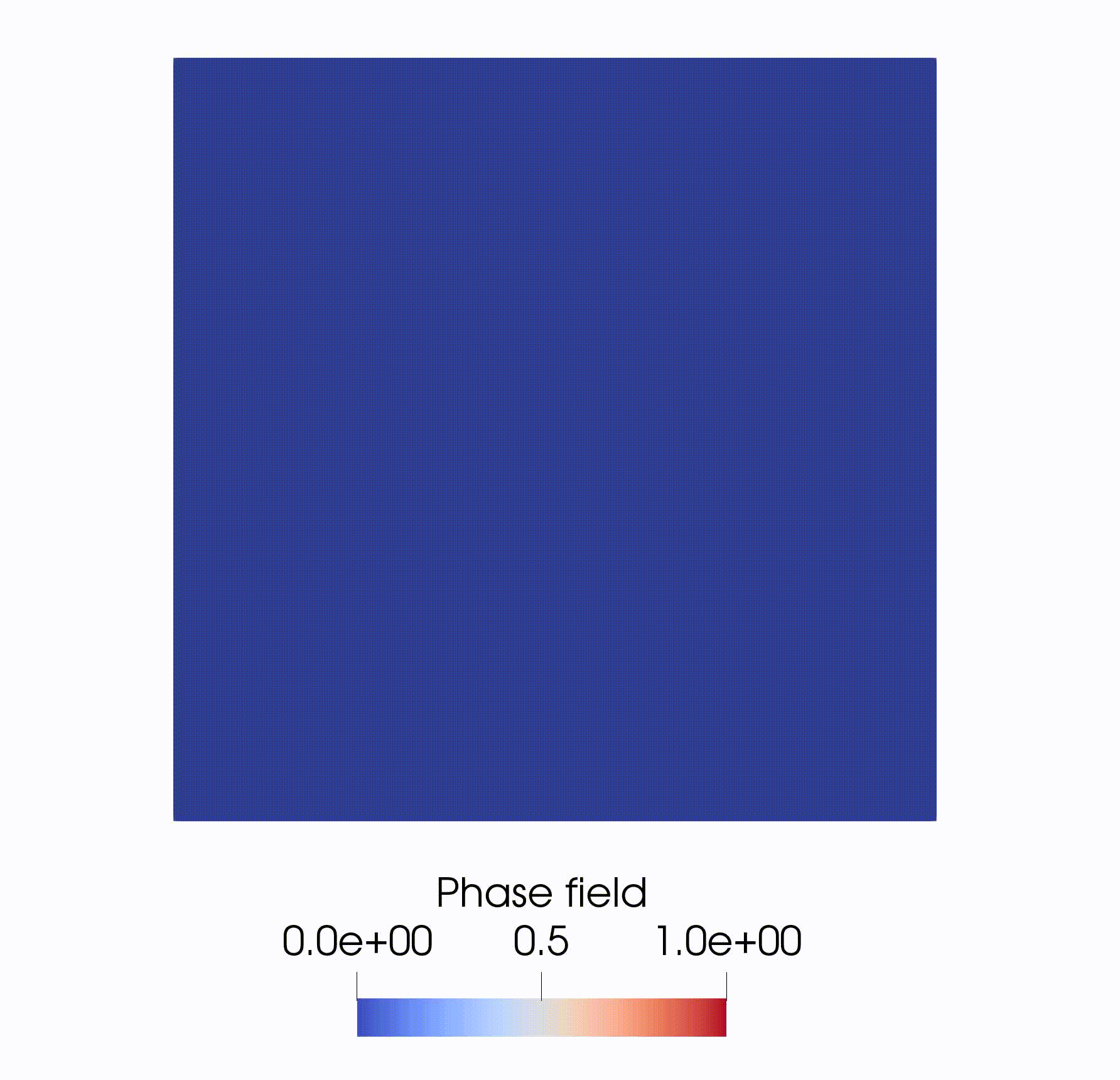
Mechanical fracture
Finite elements and phase field are computational techniques used in mechanics. Finite elements break down complex structures into smaller elements for analysis, while phase field methods model phase boundary evolution in materials. Together, they provide a powerful means to efficiently analyze and understand intricate mechanical phenomena in engineering and materials science
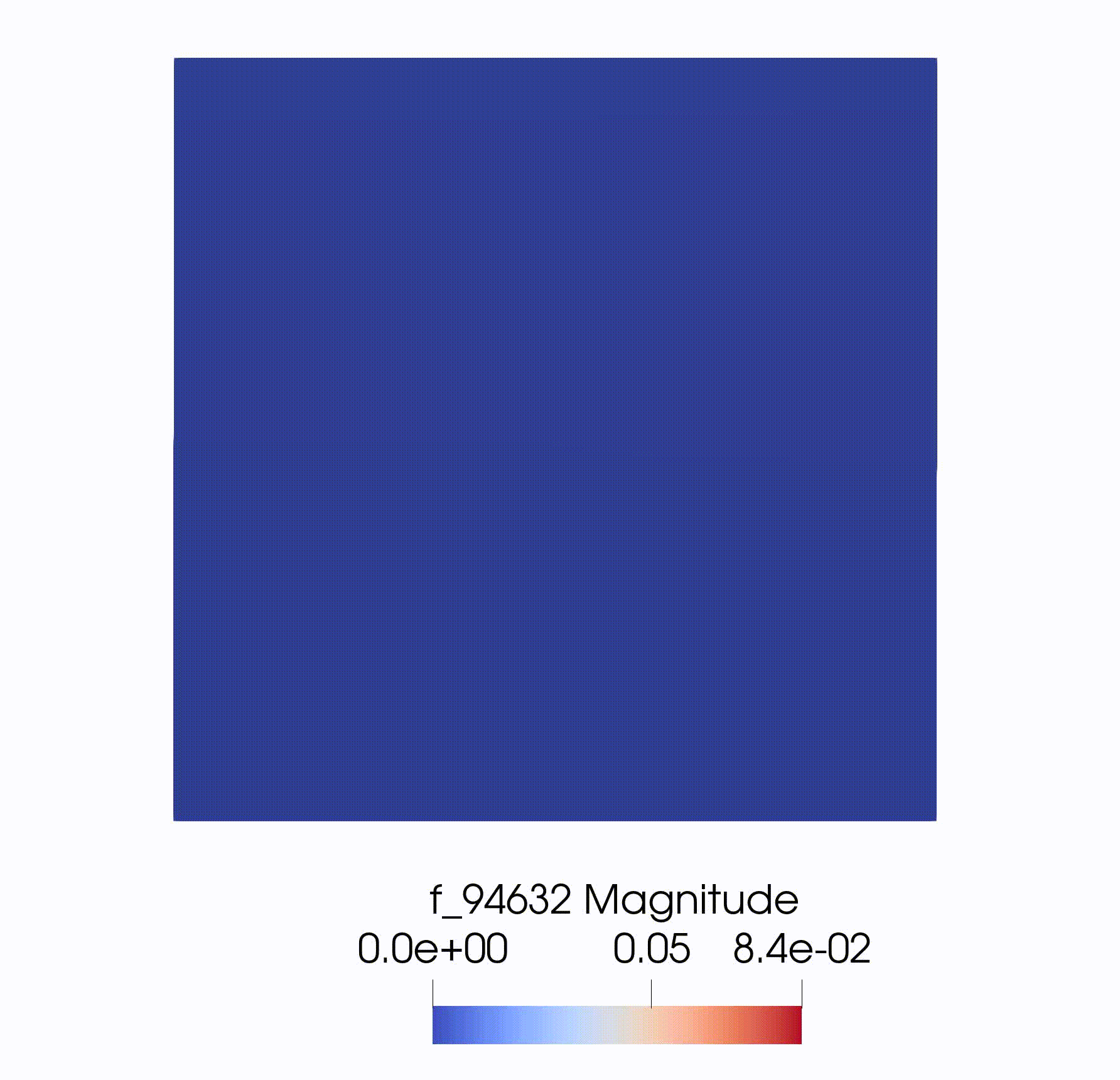
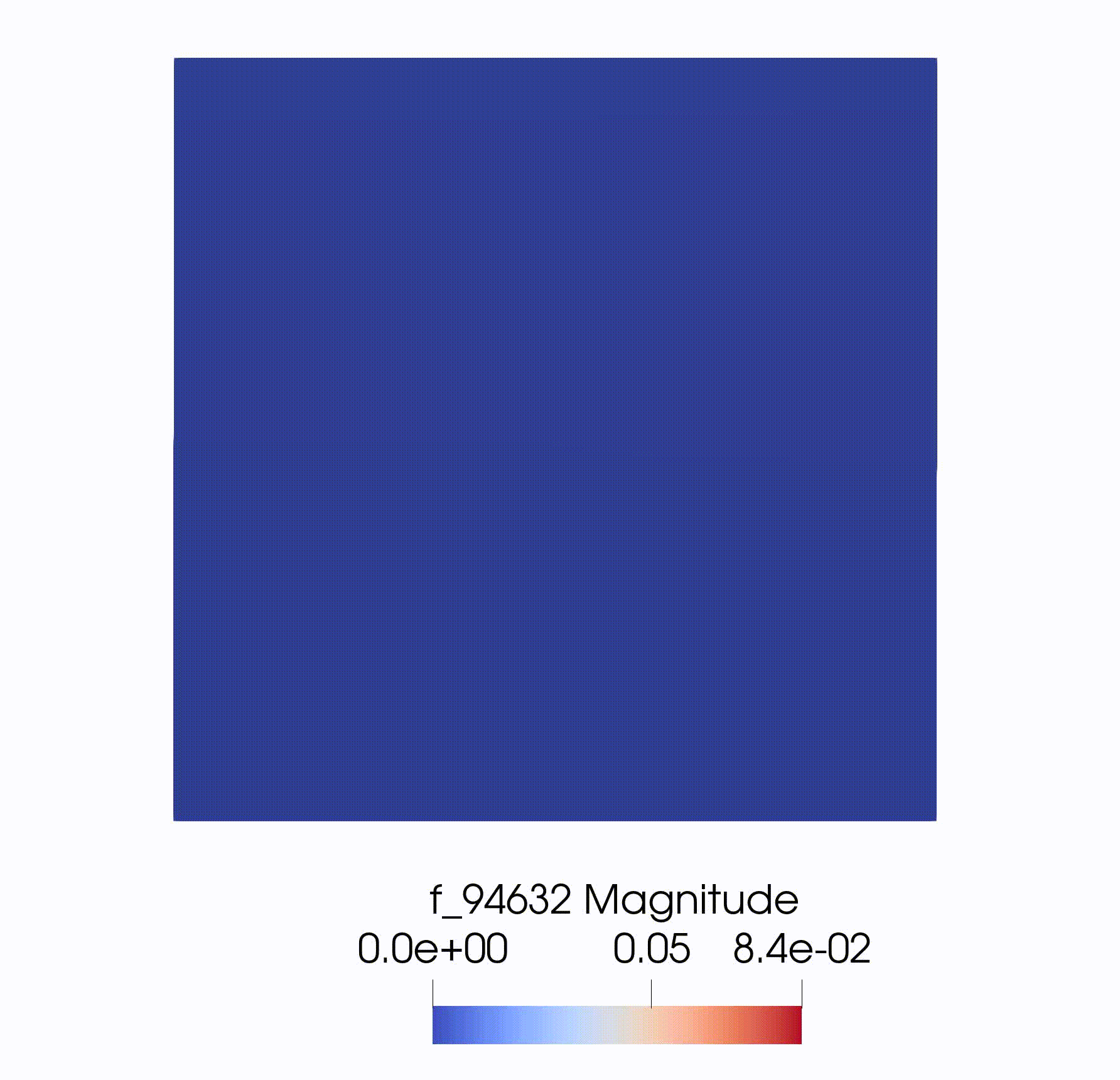